Linx: Integrating a complete end-of-line solution
As a specialist integrator of end-of-line automation, we’re renowned for maximising production line efficiency for our customers. Our range of industry-leading products are all designed to work together as a modular system, and in this case study, we uncover how we provided just that for Linx Printing Technologies.
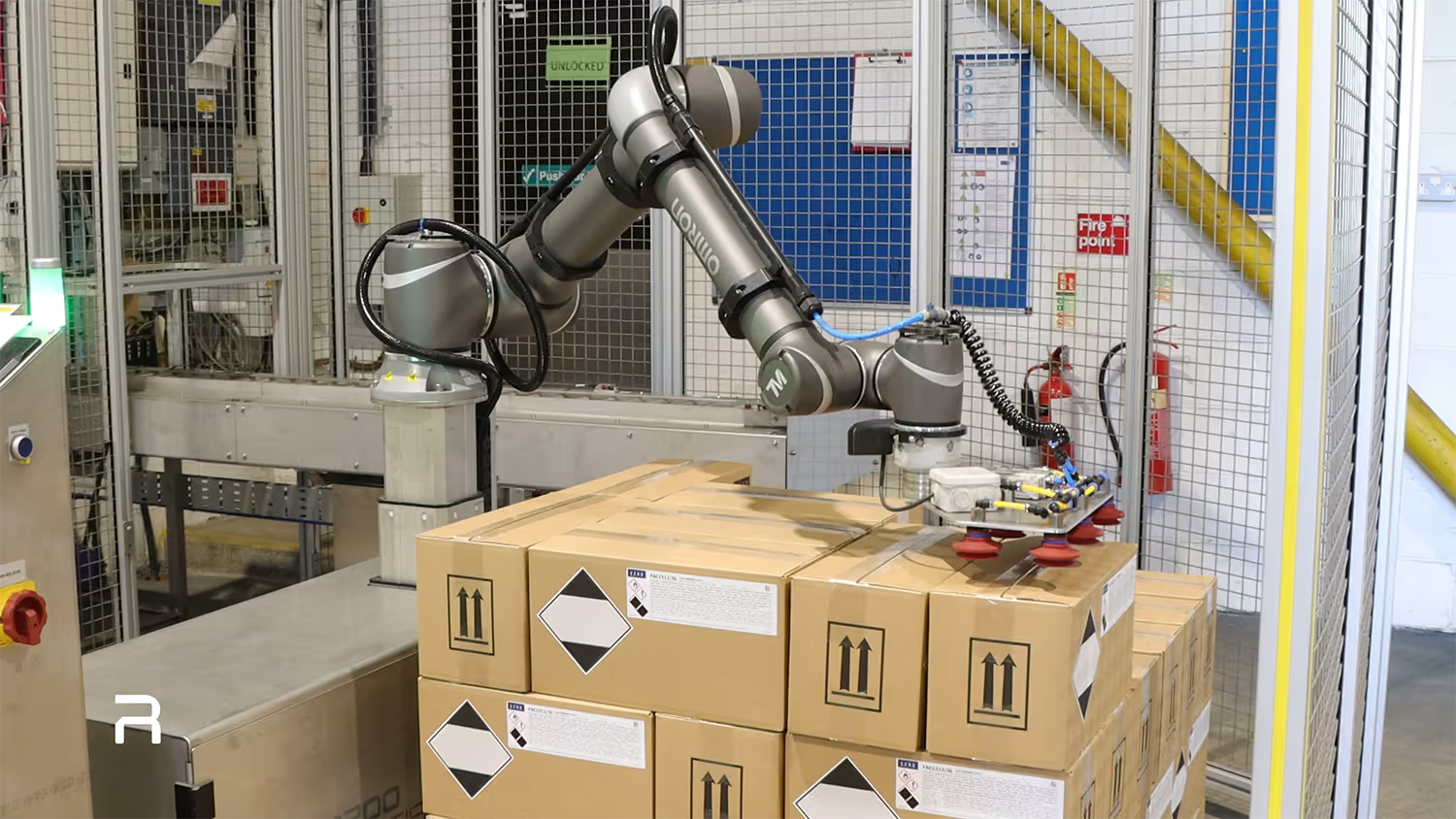
Background
Headquartered in St Ives, Cambridgeshire, Linx Printing Technologies has been at the forefront of the printing technology industry since 1987 and is a truly global operation, with distributors in over 100 countries around the world. Any industry requiring product identification codes, batch numbers, use-by dates, and barcodes likely relies on a Linx printer. Their continual innovation in continuous inkjet printing benefits from the latest advancements in production line technology — and that’s where Reeco comes in.
The challenge
Maximise accuracy and throughput whilst prioritising safety
Linx was looking to review the efficiency and safety of their solvent production line. As a line that handles the packaging and palletising of hazardous liquids, safety was a high priority. As well as health and safety, the improved production line would need to streamline each stage of product transfer to improve throughput based on demand.
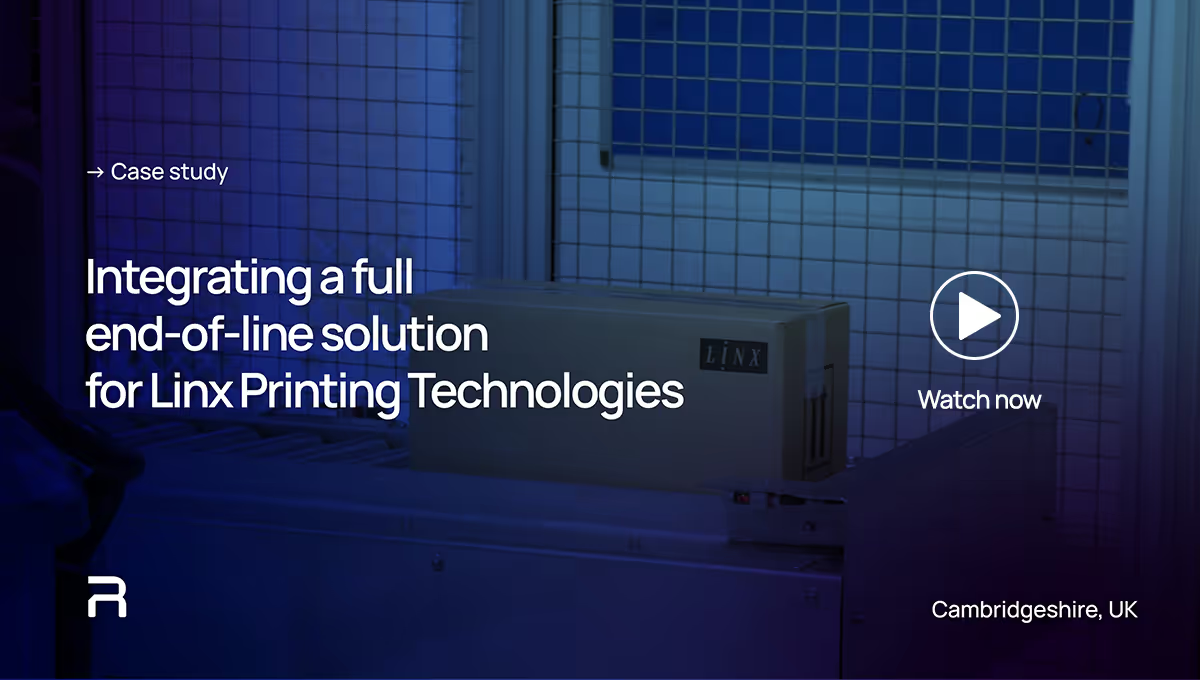
“Our previous packing process lacked efficiency, particularly when it came to palletising. We had a manual process, which involved 8-hour shifts of manual packing and palletising. We reached out to Reeco to discuss the viability of integrating an automated system at our production facility.”
The Reeco solution
After a visit to Reeco’s headquarters for equipment demonstrations and detailed discussions around implementing automation, Linx commissioned Reeco to undertake an in-depth review of the end of their solvent production line. We worked closely with Linx to deliver a solution that automated their case erecting, case packing, and palletising functions with cobot technology, complete with smart conveying between each stage.
We consulted on a layout reconfiguration for Linx, tailoring the entire process to be as efficient as possible within the physical space available, successfully spanning two separate buildings on different levels — an additional layer of complexity.
“Reeco worked closely with us to review our previous production line layout, suggesting where automation could be implemented to increase throughput. It was clear to see how Reeco’s automation could reduce manual handling, from product packing all the way through to palletising.”
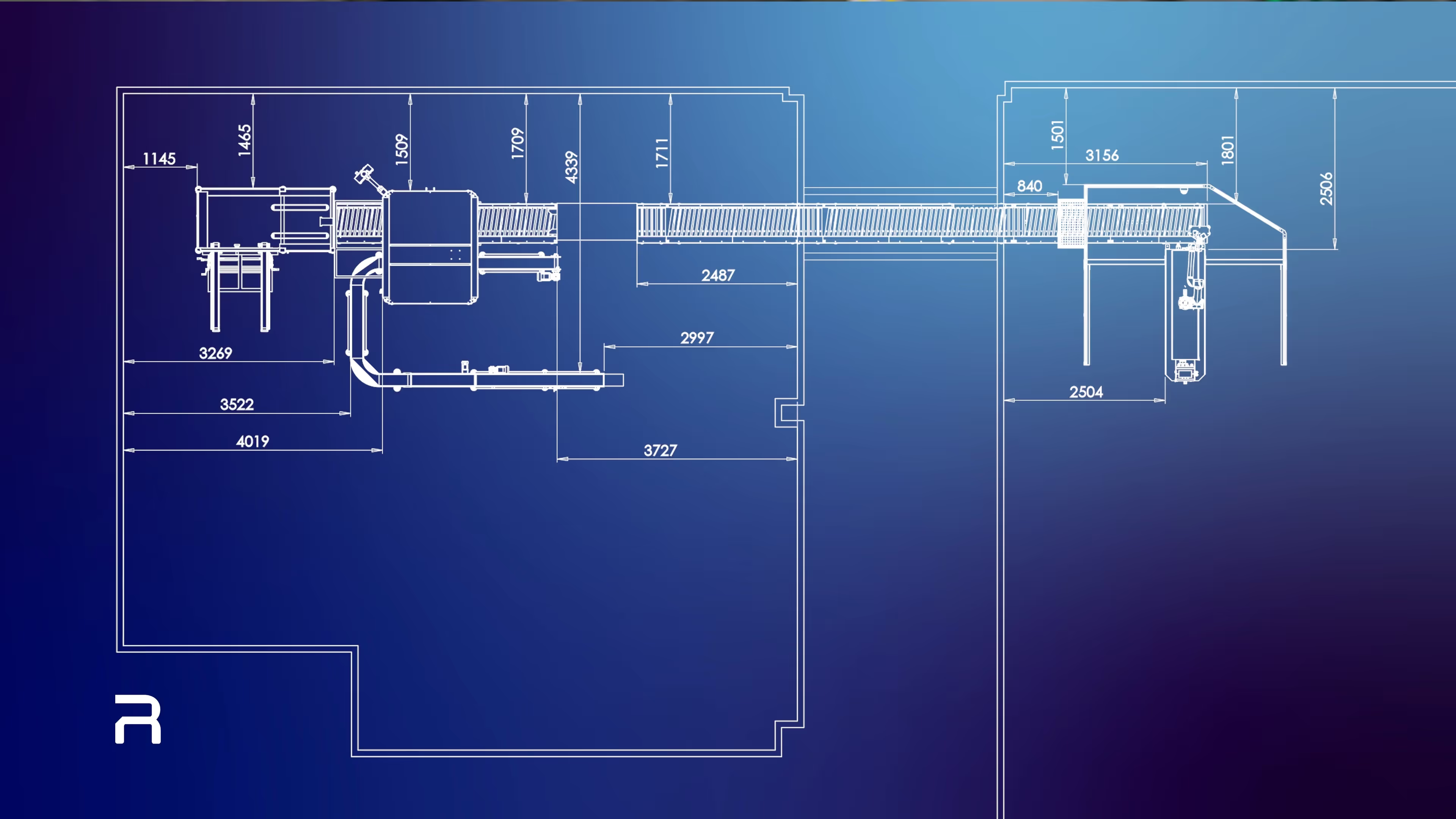
Production line walkthrough
The production line begins in the packing hall with our automated case erecting and case packing. 1-litre bottles of solvent arrive in single-file on this custom-built mesh conveyor belt with a lift-up section for service access.
The Reeco CP600 Case Packer, equipped with a bespoke end-of-arm tool, grips, lifts and places five bottles simultaneously into boxes at a rate of 25 bottles per minute. Although it’s capable of nearly double this speed, this CP600 has been optimised to handle hazardous solvents and adjust throughput based on demand.
Open boxes then pass through a manual station where cardboard inserts are added and the cases are then sealed. The boxed products are then fed along a custom-built inclined SmartConveyor, through an integrated labelling stage which applies hazard labels to them in-transit, before they ascend through to the next building.
Finally, the boxes are palletised by Reeco’s flagship RB Palletiser, in this case a single-bay RB1200. The integrated OMRON cobot arm orientates boxes with labels outward to meet regulatory requirements. EasyStack software simplifies palletising, while perimeter guards and sensors ensure safety by halting the arm if thresholds are breached.
“We’ve been very impressed by Reeco’s thoroughness at every stage. Their end-of-line automation has increased our throughput capacity, as well as bringing improvements to our overall health and safety. Reeco took care of everything, from detailed planning to installation, including direct communication with civil works. The entire project was completed within six months, and the end result speaks for itself — it’s maximised the accuracy, speed and efficiency of our production line.”
————
If you’d be interested to learn more about how cobot technology can transform your end-of-line production, speak to our specialists today.
You may also be interested in
Two companies delivering one solution
In the face of an increasingly challenging human resource situation in the UK, with manual labour shortages and higher wage bills, more and more businesses are turning towards automation as a reliable way of scaling up. Two companies, Reeco and Somic, have found a perfect synergy delivering automated solutions to end-of-line processes where wraparound packaging is involved. Both are specialists in their own field, delivering innovative high-tech solutions that help businesses to drive cost savings, boost profitability and achieve sustained growth in a challenging economy period.
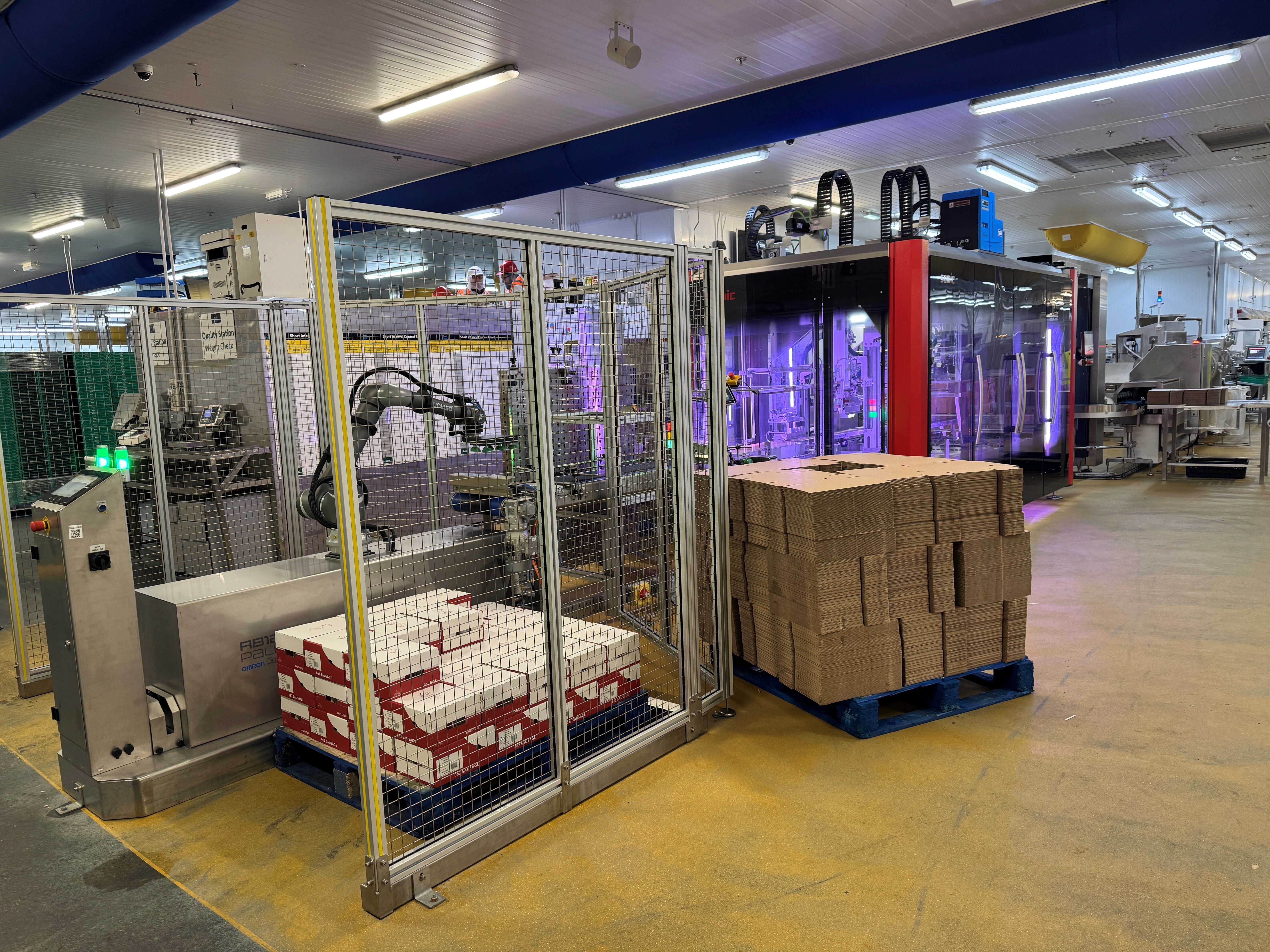