The Reeco & OMRON Partnership
As we look back on five years of our successful partnership with OMRON, we thought it would be good to review how the partnership began and has flourished since. In this article, we tell that story and look specifically at how the two companies came together to build significant market presence with the groundbreaking RB Series Palletiser.
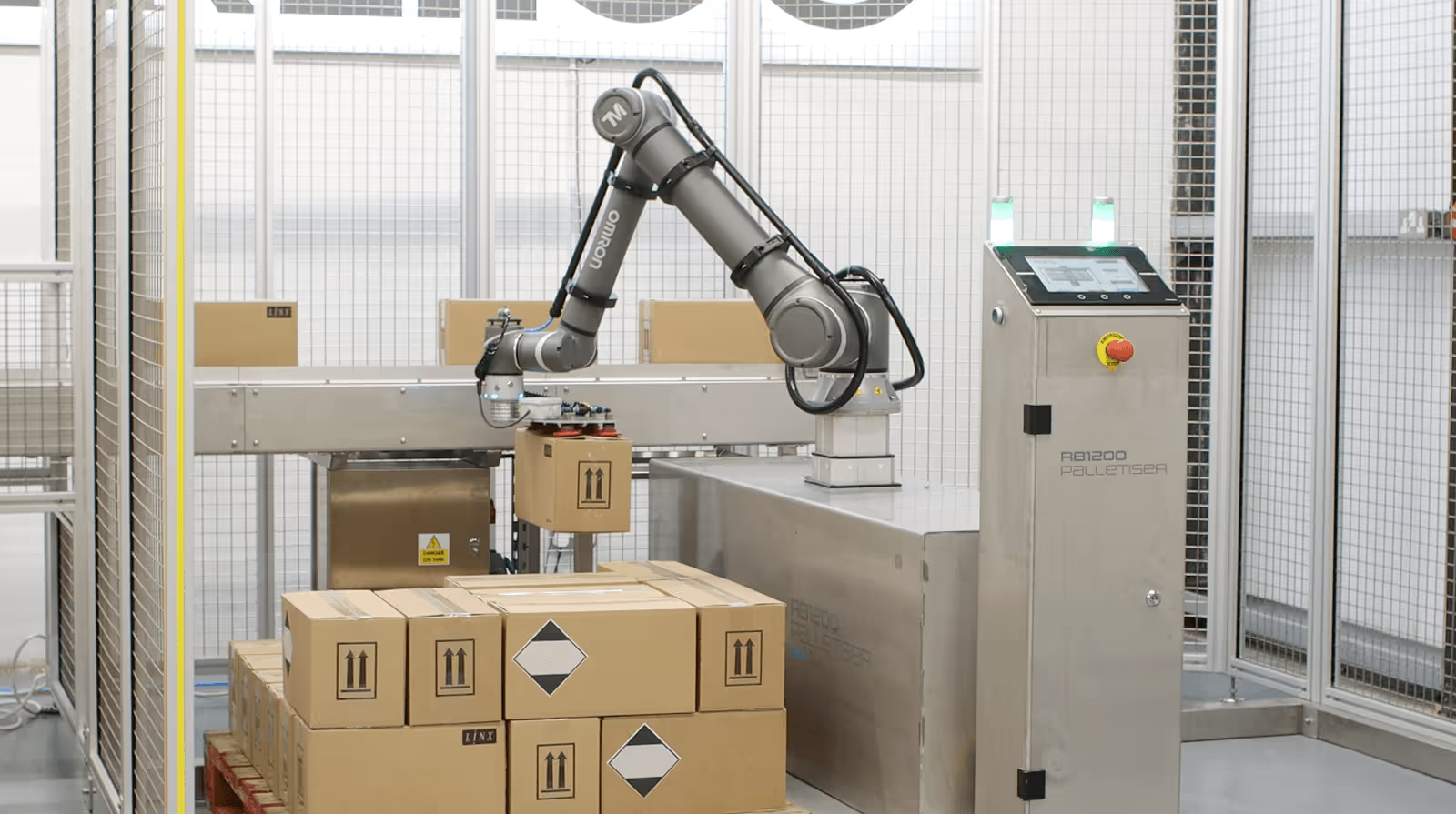
Company Profile (Reeco and OMRON)
Reeco Automation is a specialist UK-based integrator of cobots, automating the transfer of products from production line to dispatch. It was founded in 2016 by Llewelyn Rees, who had over 20 years’ experience in robotics and industrial automation. He was quick to see the potential that cobots had to transform end-of-line processes and make automation accessible to smaller manufacturing facilities. The company has grown rapidly and quickly established an enviable track record of successfully integrating automation into customers’ systems.
OMRON is a multi-billion-dollar global leader in the development and manufacture of electronics and automation technologies. Since its founding in Japan nearly 100 years ago, OMRON’s business has grown to provide products and services in more than 130 countries.

How the OMRON and Reeco paths crossed
The background to the Reeco/OMRON partnership was a classic one of good fortune. Reeco was an established leader in the UK cobot market, with significant technical expertise in the field. OMRON recognised that cobots were a fast-growing market and were looking to grow the presence of their cobot offering in the sector.
Then entered multinational giant Unilever. They had a global relationship with OMRON for use of their products and also used Reeco’s system integration expertise within the UK. Unilever recognised the potential synergies from the two working together to achieve some of their desired automation objectives and acted as matchmaker, introducing OMRON and Reeco to each other in 2019. The ensuing positive collaboration resulted in wider discussions between the two companies. And this led in 2020 to OMRON appointing Reeco to the OMRON Solution Partner (OSP) network to work together on building cobot solutions that maximised ROI for their customers.
What was the challenge?
The challenge for Reeco and OMRON was how to make a strong market entrance in the UK with their cobots, when other manufacturers had already achieved strong market recognition. Llewelyn believed that creation of a specific cobot-based automation solution would gain greater traction than simply offering ‘bare cobot arms’.
OMRON’s vast market research capacity helped to validate the different options that were then considered. The result was an agreement to focus on cobot palletisers, a market need that Llewelyn had identified as being very poorly met by existing products on the market.
Traditional robot palletisers take up considerable floorspace and can take months to install. It is then hugely expensive to disassemble and reassemble in another location, should the demands of the business change. The purchase and installation costs put them beyond the reach of all but large companies.
This size and inflexibility had been recognised by other market players, leading to the development of more nimble solutions in the shape of cobot palletisers. However, OMRON and Reeco identified several issues with these existing cobot palletisers.
First and foremost was the safety aspect. Unlike traditional industrial robots, cobots are designed to work in close proximity to workers carrying out manual processes. At that time, other cobot integrators felt that this meant they didn’t need safety measures, such as interruption sensors or safety fencing, and it was clear that thorough risk assessments were often being sacrificed in the drive for sales. This clearly did present a risk, and subsequent H&S inspections would often condemn such solutions.
Secondly, existing cobot palletisers required expert users with sufficient specialist knowledge to interact with the onboard computers that managed the cobot’s operations. In addition, the internal computers were not sufficiently powerful to provide the flexibility that would have made the palletisers fully effective.
Finally, the auxiliary equipment and tooling for existing palletisers was poorly designed. OMRON and Reeco recognised that a complete solution was required that would maximise their palletiser’s productivity and therefore the value for customers.
What was the solution?
The partnership between Reeco and OMRON facilitated the development of the ground breaking RB Palletiser, a cobot-based automation that addressed all the shortcomings of existing palletisers on the market.
First off, safety is inherent in the RB Palletiser, which uses OMRON optical laser scanners to monitor the surrounding area and halt operations if potential human contact is detected. It also comes with safety fencing as standard, suited to the specific configuration provided, and based on the full risk assessment that Reeco performs as part of its integration service.
Then there’s the operational simplicity. Product, pack, and layout configuration changes can be swiftly executed using Reeco’s EasyStack visual software, requiring minimal programming skills or robot experience. All this is operated from the user-friendly touch screen within the operator station, requiring no external devices to control the palletiser. And the inbuilt OMRON industrial PC makes the RB Palletiser powerful enough to handle more complex routines than any other known cobot palletiser.
The cobot’s arm can be fitted with either a vacuum head or Reeco’s unique Servo-grip head, capable of handling over 90% of box-based products. Most adjustments to suit product types can be effected via the touchscreen, but where a change of physical tool is required, it can be done within minutes. And for special applications, Reeco offers custom-designed or adapted tooling to accommodate non-standard packing requirements.
Another central feature of the RB Palletiser is its compact size, which makes it fast and easy to re-deploy by pump truck to another line as production requires. A far cry from relocating a traditional robot palletiser within a factory, which involves a substantial logistical effort and considerable time investment.
The contrast with traditional robots is also apparent at initial installation. Where traditional robots often require months for deployment, the RB Palletiser comes with an installation timeline of 2-3 weeks from order to completion. And the plug-and-play operation reduces actual installation time to as little as 1-2 hours, causing minimal interruption to production.
These benefits are all significant, but they are complemented further by a cost that is up to 50% lower than traditional robot palletisers. Once in place, the RB Palletiser typically pays for itself within a few months, which can be proven by the comprehensive efficiency data that it delivers in real time.
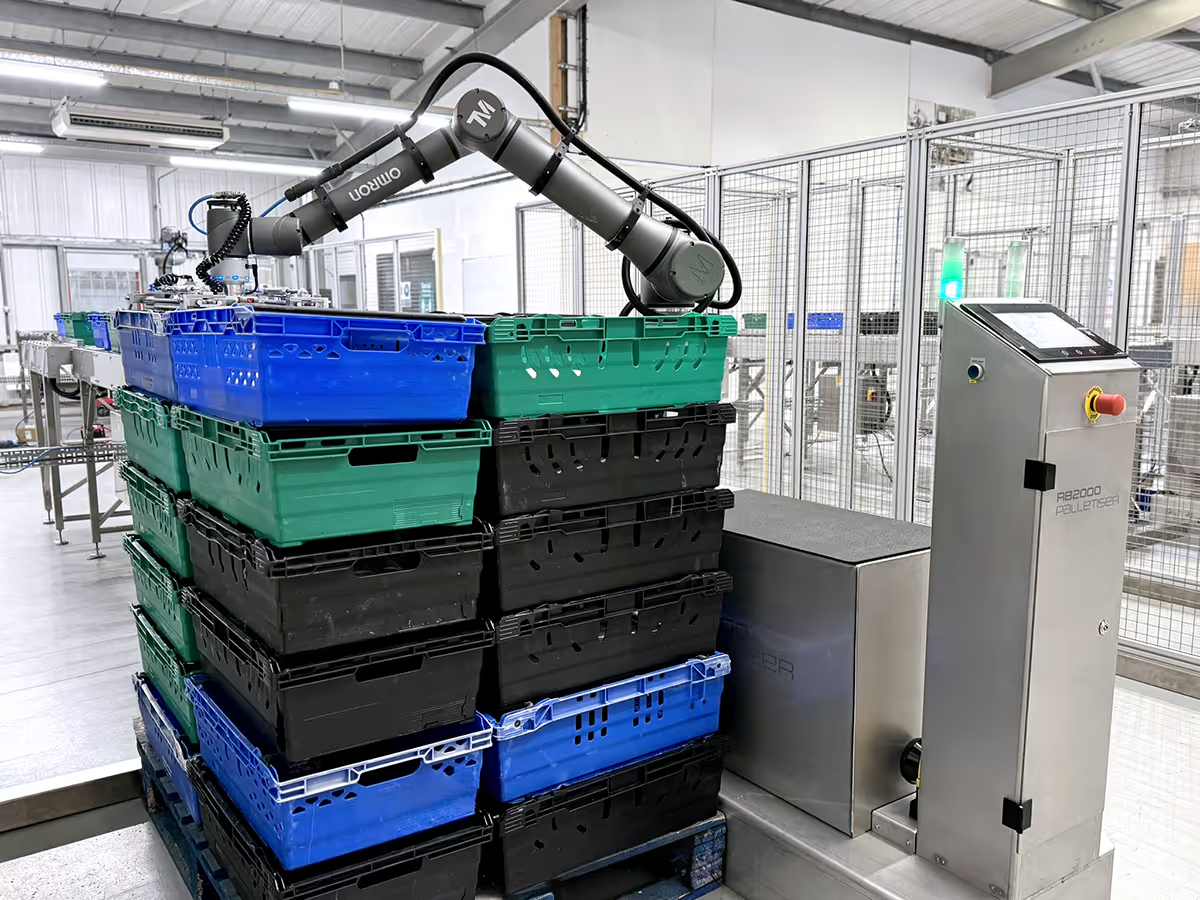
What was the outcome?
The RB Palletiser makes robotic palletising an attractive and feasible option not just for large companies but for SMEs and smaller manufacturing sites as well. Throughout the RB Palletiser’s development, Reeco and OMRON focused on how to remove the risk from the customer’s investment and maximise their returns.
The collaboration is a perfect commercial partnership, with each company offering unique and complementary attributes. Neither company could have achieved the success associated with the RB Palletiser without each other’s input.
Reeco provided the technical expertise in design and integration of cobot technology to achieve the desired result. Development of the unique and user-friendly software harnessed the power of the cobots and converted it into a ready-to-use automation solution. Engineering of the unique Servo-grip head maximises the functionality and versatility of the palletiser for varied applications.
OMRON provided expertise and training to enable Reeco to extract the maximum performance from its cobot technology. In the early days, it funded the building of two demonstration RB Palletisers and hosted them at their Milton Keynes showroom, which customers could see and trial with their own products. Other marketing support, from early research through to its promotion by the extensive OMRON sales team, supported the product’s launch and subsequent success.
The OMRON/Reeco partnership has not just led to a product that opens up automation to a wider range of companies. It has also enabled both companies to successfully carve out end-of-line automation as a niche area of the cobot market within the UK, with further expansion into Europe already underway.
"Reeco’s ability to overcome customer challenges, has been particularly impressive whilst consistently innovating and de-risking projects to ensure a successful outcome for all parties. Reeco’s dedication to excellence have set a high standard within UK manufacturing. Reeco’s positive attitude and collaborative spirit make them a joy to work with. We are grateful for our partnership and look forward to many more years of success together."
You may also be interested in
Reeco’s RB Lite Palletiser Offers Scalable Automation for Smaller Lines
Reeco’s newest palletising system, the RB Lite Palletiser, is designed for manufacturers looking to automate smarter, without the scale, cost, or complexity of a full-sized cell.