Automation collaboration for bespoke solutions that maximise ROI
Reeco Automation supplied Grace Foods UK with an RB2000 Palletiser to support its production demands. With a fully-integrated Reeco palletiser, the company has reduced labour at the end of the line by up to 20%, along with increased throughput and reduced downtime.
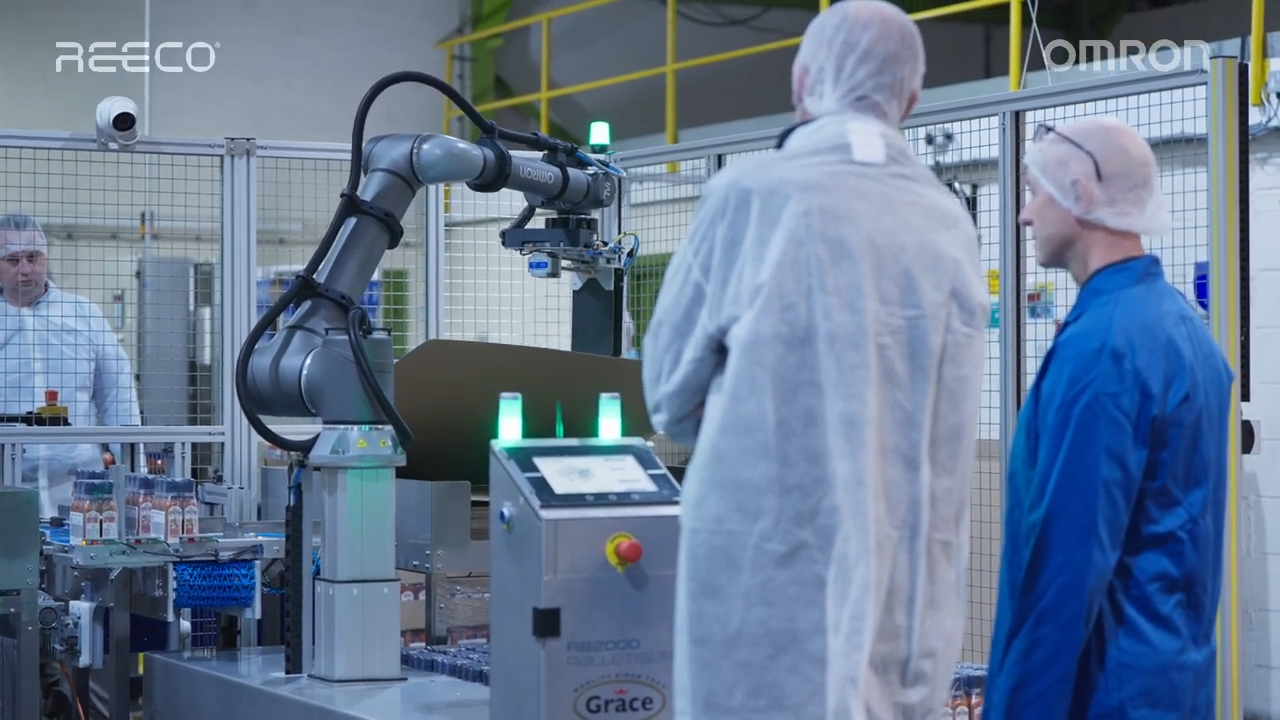
Eliminating downtime
By adopting a robot palletiser, one food manufacturer has eliminated downtime, significantly increased throughput, and reduced the number of staff needed on the task by 20%, allowing them to be redeployed to other areas.
Grace Foods UK, which produces everything from sauces to powders and pulses for the catering and retail industry, worked with OMRON Electronics and Reeco Automation to help boost the efficiency of its processes.
“We had a pot of money to invest in kit that would deliver return on investment (ROI),” said Tony Carter, Engineering Manager at Grace Foods. Loading pallets is a physically-demanding manual task – exactly the kind of role the manufacturing industry is currently finding difficult to fill. As such, Grace Foods “considered the robot palletiser to be the best option”.
While adopting such a solution is “quite simple in theory”, explained Phil Perry, Technical Sales Manager at Reeco, it is actually quite challenging. “There are a lot of SKUs, and there's a lot of information to absorb,” he went on. “We worked collaboratively with the customer to get the right application and the right solution onto the shop floor, to make sure the product leaves the line in the best state possible.
“Once we had all the information, we put forward the RB2000 with the layer card option, so we could remove the people from the end of the line, and the company could utilise those staff elsewhere.”
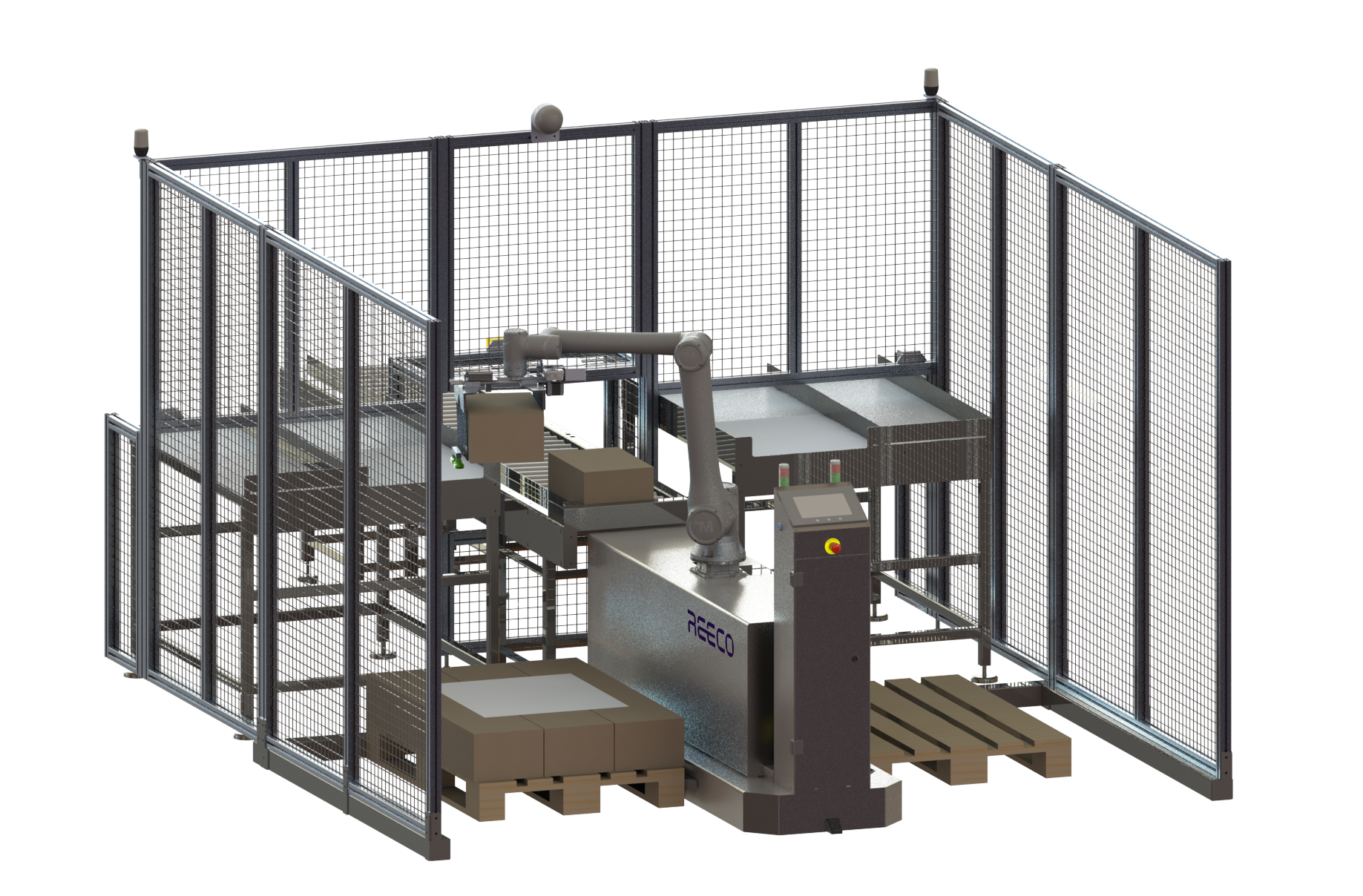
A unique solution
Robert Meechan, System Integrator Manager at OMRON, said the solution was specifically designed to meet Grace Foods’ needs.
“The obvious part you see when you look at the palletiser is the robot arm. But it's much more than that. We've worked with Reeco to design the inside of the robot, and everything – the safety scanner sensors, the servomotor and the interface – is connected on the OMRON Sysmac platform,” he explained.
“Everything talks on one simple network, and we've co-developed the software for the operating system, which makes it a very flexible and adaptable system. It only takes a few minutes to change the palletiser over to work with different products.”
Carter said the solution had reduced the number of people required to run the line by 20% and provided added efficiencies and a faster throughput.
“Thanks to the reliability of the kit, we do not incur any downtime”
Carter said, adding that the solution had removed the manual handling element of the task, making it safer for staff.
That all-important reliability is further compounded by Reeco’s ongoing support. “Every system we put out has remote access. If there are any issues, we can fix most of them from our base. If we need to get out to the customer, we can do that as well.”
A collaborative approach
By working with OMRON and Reeco, Grace Foods was able to secure a bespoke solution, designed to meet the factory’s specific needs.
“We've now got a fully operating robot palletiser that's producing the efficiencies we need here on site to achieve ROI. It’s all been very positive.”
Watch the video
See the Reeco RB2000 Palletiser in action as part of the video case study below.
You may also be interested in
Linx: Integrating a complete end-of-line solution
As a specialist integrator of end-of-line automation, we’re renowned for maximising production line efficiency for our customers. Our range of industry-leading products are all designed to work together as a modular system, and in this case study, we uncover how we provided just that for Linx Printing Technologies.
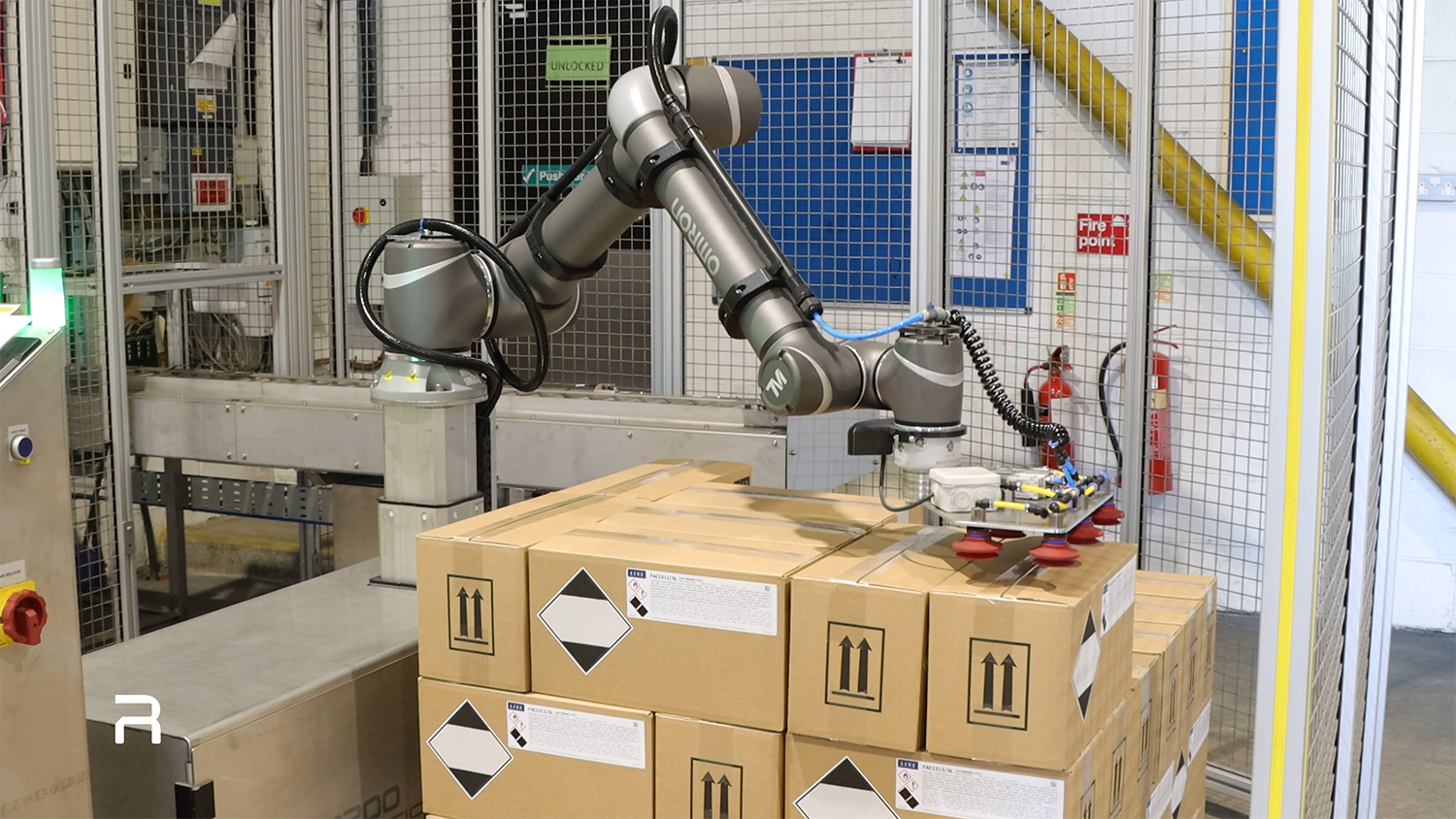