Centralised vs localised palletising: Which is best for the end of my production lines?
The move towards end-of-line automation has been accelerated by changes in the labour market post-Brexit. The reduced access to overseas workers has resulted in a smaller pool of manpower and rises in the statutory minimum wage has also increased the cost of labour. This has all added to the existing arguments of enhanced productivity and reliability for switching to automated processes.
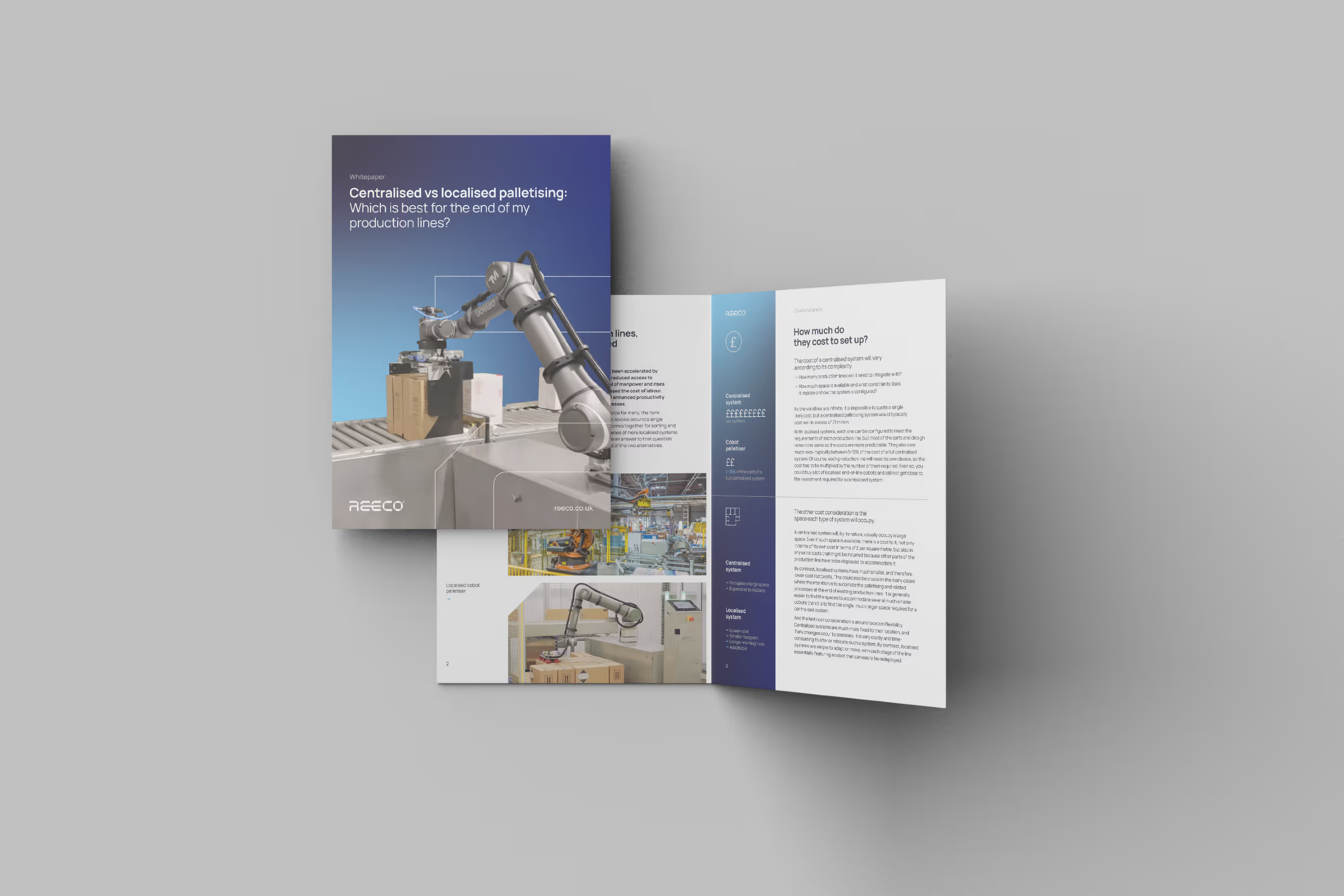
But if automation has become a more obvious choice for many, the form it should take is sometimes less obvious. Should it revolve around a single centralised system, where each production line comes together for sorting and palletising at the end of the process, or would a series of more localised systems deliver more? This whitepaper attempts to provide an answer to that question by considering the different features and benefits of the two alternatives.
Click to read the PDF version >
How much do they cost to set up?
The cost of a centralised system will vary according to its complexity.
– How many production lines will it need to integrate with?
– How much space is available and what constraints does it impose on how the system is configured?
As the variables are infinite, it is impossible to quote a single likely cost, but a centralised palletising system would typically cost well in excess of £1 million. With localised systems, each one can be configured to meet the requirements of each production line, but most of the parts and design remain the same so the costs are more predictable. They also cost much less– typically between 5-10% of the cost of a full centralised system.
Of course, each production line will need its own device, so the cost has to be multiplied by the number of them required. Even so, you could buy a lot of localised end-of-line cobots and still not get close to the investment required for a centralised system.
The other cost consideration is the space each type of system will occupy.
A centralised system will, by its nature, usually occupy a large space. Even if such space is available, there is a cost to it, not only in terms of its own cost in terms of £ per square metre, but also in any extra costs that might be incurred because other parts of the production line have to be displaced to accommodate it.
By contrast, localised systems have much smaller, and therefore, lower-cost footprints. This could also be crucial in the many cases where the intention is to automate the palletising and related processes at the end of existing production lines: it is generally easier to find the spaces to accommodate several much smaller cobots than it is to find the single, much larger space required for a centralised system.
And the last cost consideration is around location flexibility. Centralised systems are much more fixed to their location, and if any changes occur to premises, it is very costly and time-consuming to alter or relocate such a system. By contrast, localised systems are simple to adapt or move, with each stage of the line essentially featuring a cobot that can easily be redeployed.
How much do they cost to run?
Again, because centralised systems are so variable, it is impossible to say how much any given one will cost to run. What is certain about localised systems is that they require surprisingly little power to operate. As an example, one of Reeco’s RB palletisers uses electricity at about the same rate as it takes to boil a kettle.
Which can handle the greater throughput?
In this instance, centralised systems definitely come out on top. They comprise larger machines that can handle much higher volumes of product. However, what really matters is matching the handling capacity of the system with the volumes of products coming through. There is no point in paying for a system that can handle volumes that run into millions if it will only be seeing much lower numbers. The last thing your automated system should be doing is lying idle while it waits for products to handle! There is also another key aspect to productivity that can shift the balance in favour of localised system.
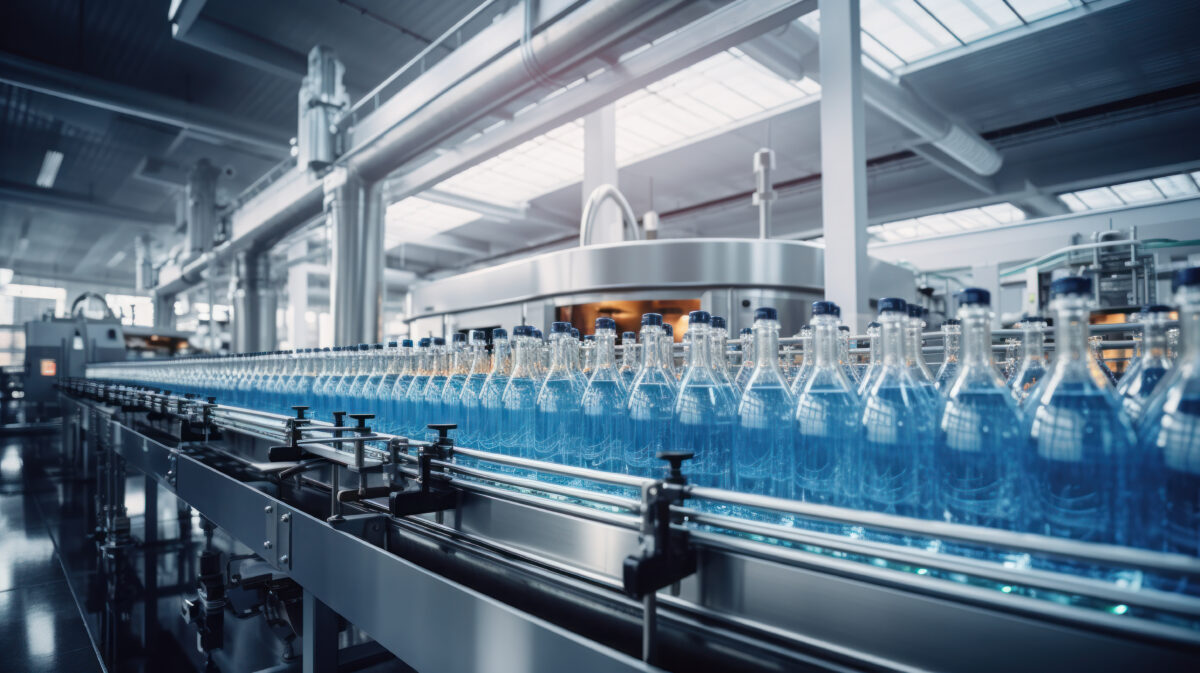
What happens in the event of a service disruption?
In a centralised system, because all the production lines are feeding into the same end-of-line process, any stoppage will affect the whole production line. For example, if the system needs to be adapted to accommodate revised packaging, everything will have to come to a stop while the system is modified. With a localised system, only one production line is affected at a time and modifications can often be carried out in minutes through on-board software (as is the case with Reeco’s RB palletisers, for example).
Likewise, if a fault with the system occurs that brings it to a halt, production everywhere leading into a centralised system has to cease until the fault has been fixed.
The complexity of centralised systems is also such that it typically requires an expert to investigate any fault and effect a repair. The cobots used in localised systems are more standardised and as a result more easily fixed, often by non-experts using the machines’ own on-board diagnostic and self-repairing software. Even in the event of a fault requiring more major intervention, it is much easier for a business to revert temporarily to manual handling relative to one production line than it is to do so relative to multiple production lines, which is what would happen with a centralised set-up.
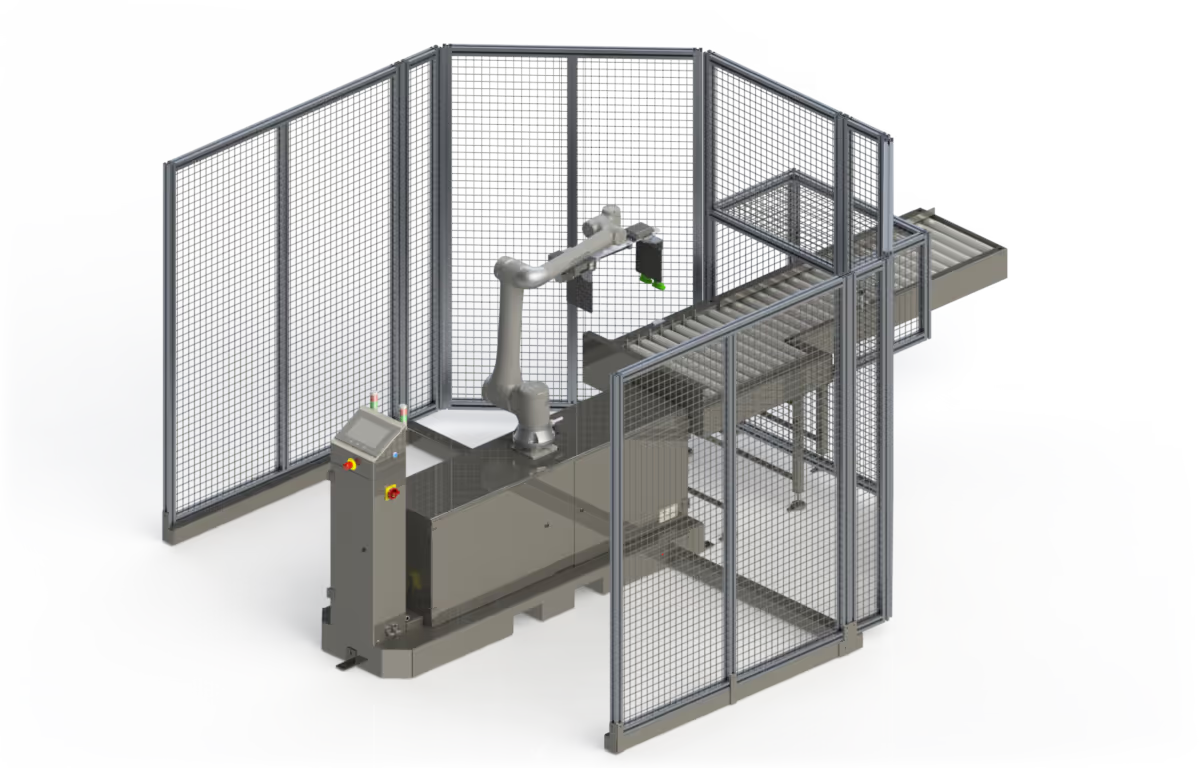
How adaptable are they?
By their nature, centralised systems are set up to handle a large number of products in packaging that comes in one, or limited number, of forms. Hopefully, the packaging will not change much, if at all, but none of us can be sure what the future might bring. Even if a business has no intention of altering the packaging around its products, it may be obliged to by changes in laws or regulations.
Localised systems are much more adaptable. Indeed, flexibility is one of their key attributes, with many updates being possible simply through a simple update to their onboard software, or by swapping one tool at the end of a cobot arm for another.
In summary: Centralised or localised?
Where products are produced in very high volume and in standardised packaging, a centralised system will normally be the preferred option. For example, many different food products end up packaged in standard-sized aluminium cans, so it makes sense for them all to ultimately end up in the same packaging system.
However, in cases where the products involved have greater variability and/or the throughput rate is lower, the benefits of localised systems as described above make them generally the better option. And, in fact, full end-of-line automation can be achieved with localised systems, using conveyors and AMRs to transport goods between cobot-automated case erecting, packing and sealing, through to palletising, and then AMRs (Autonomous Mobile Robots) to take the pallets to their next destination.
In conclusion, the right answer to the question, ‘centralised or localised’ will depend on the nature of your products and production requirements, but we hope this article has set out clearly the different aspects of each to be considered in arriving at the answer for your own production needs.
_
Speak to the specialists
To find out more about how Reeco can transform your end of line productivity, please call our head office on 01686 621 138, or email sales@reeco.co.uk.
You may also be interested in
How Case Packing Software Enables Manufacturers to Overcome SKU Challenges
Throughout all industries, there are tasks which are perfect for automation, allowing human dexterity and creativity to be better utilised in a time of labour shortage. Repetitive tasks are the best subjects for automation, providing unmatched throughput and consistency and allowing manufacturers to not only better utilise operators, but significantly improve performance. Packing and other areas at the end-of-line, such as case packing, are rich in repeatability and ripe for automation.
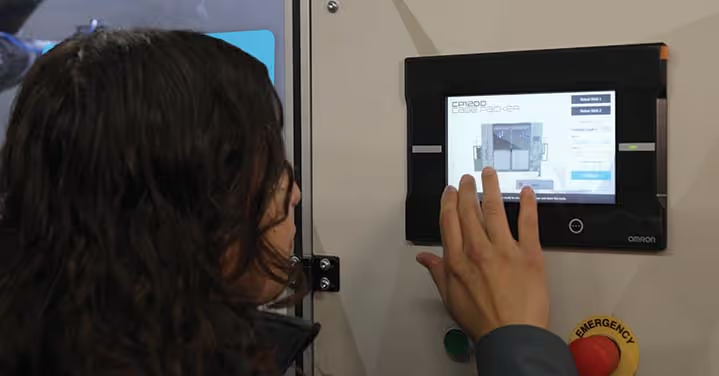