How Case Packing Software Enables Manufacturers to Overcome SKU Challenges
Throughout all industries, there are tasks which are perfect for automation, allowing human dexterity and creativity to be better utilised in a time of labour shortage. Repetitive tasks are the best subjects for automation, providing unmatched throughput and consistency and allowing manufacturers to not only better utilise operators, but significantly improve performance. Packing and other areas at the end-of-line, such as case packing, are rich in repeatability and ripe for automation.
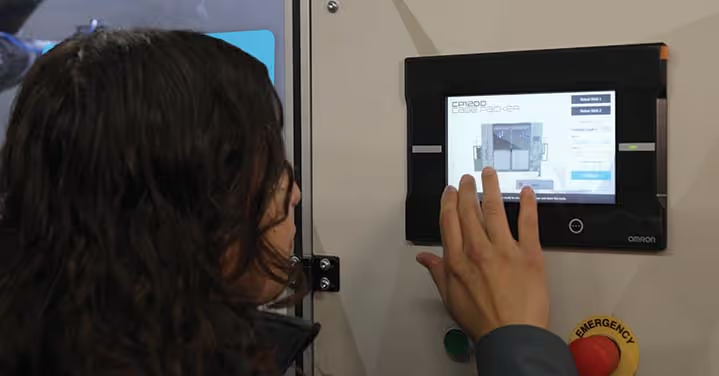
Having said this, there are increasing complexities for manufacturers in the form of variable stock-keeping-units (SKUs) and production flexibility. Prominent in areas such as consumer goods, new product activity is a key driver of sustained brand success. Historically, many choice models assume the fundamental unit for analysis when attracting new business is the brand itself, though in reality more and more decisions are being made by consumers, manufacturers, and retailers at the SKU level.
Ongoing digitalisation of shopping and the change in habits caused by covid has also had an impact. The digital revolution has handed power to consumers, giving them more information and more choice. A study by McKinsey says 40% of consumers switched brands throughout the pandemic, a side effect of the influx in digital shopping and subsequent choice/information available to consumers.
Variability in SKUs is here to stay, seasonal products, expanding product lines and catering to the consumer desire for choice are all business winning factors, but how do manufacturers optimise production for SKU portfolio complexity?
Developing and implementing the right solutions to deal with uncertain demand and product changes is paramount to a successful strategy in dealing with variable SKUs. System flexibility is a core enabler in accommodating this, the ability to use equipment on-demand and better utilise for future product changes and introductions is invaluable.
The CP1200 Case Packer
The CP1200 case packer was designed in collaboration with Omron, offering a high throughput, compact and versatile solution to case packing automation. With significantly reduced operational complexity, the CP1200 gives automation control back to the manufacturer, allowing for changes and alterations on the go.
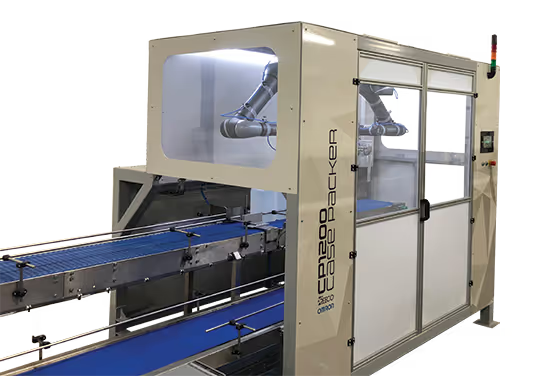
Easy Pack
Easy Pack is a user interface designed for the CP1200 case packer, a software platform which enables its users to quickly dial in any changes with no prior programming knowledge. Simplifying the complexity of automation, Easy Pack brings together all of the CP1200’s functionality into one easy to understand, visual interface.
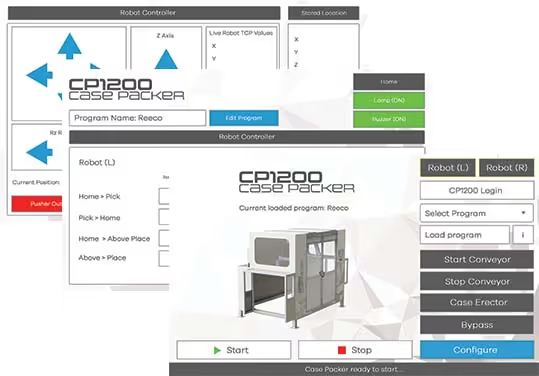
1. Changes in demand
Where manufacturers produce seasonal products, have high variable SKUs or undergo frequent production changes, Easy Pack has built in functionality for the quick change of programs to accommodate new products and packing patterns.
2. Training and Speed
Staff training on new equipment can often be lengthy, with complexity and training time required going hand in hand. Easy Pack was designed with the end user in mind, offering a visually intuitive interface which can be programmed with no prior programming knowledge.
3. Complete System Control
Easy Pack combines and interfaces all of the technology and functionalities of the CP1200, integrating robots, conveyors, tooling and other surrounding equipment into one fool-proof user interface.
_
Speak to the specialists
To find out more about how Reeco can transform your end of line productivity, please call our head office on 01686 621 138, or email sales@reeco.co.uk.
You may also be interested in
Centralised vs localised palletising: Which is best for the end of my production lines?
The move towards end-of-line automation has been accelerated by changes in the labour market post-Brexit. The reduced access to overseas workers has resulted in a smaller pool of manpower and rises in the statutory minimum wage has also increased the cost of labour. This has all added to the existing arguments of enhanced productivity and reliability for switching to automated processes.
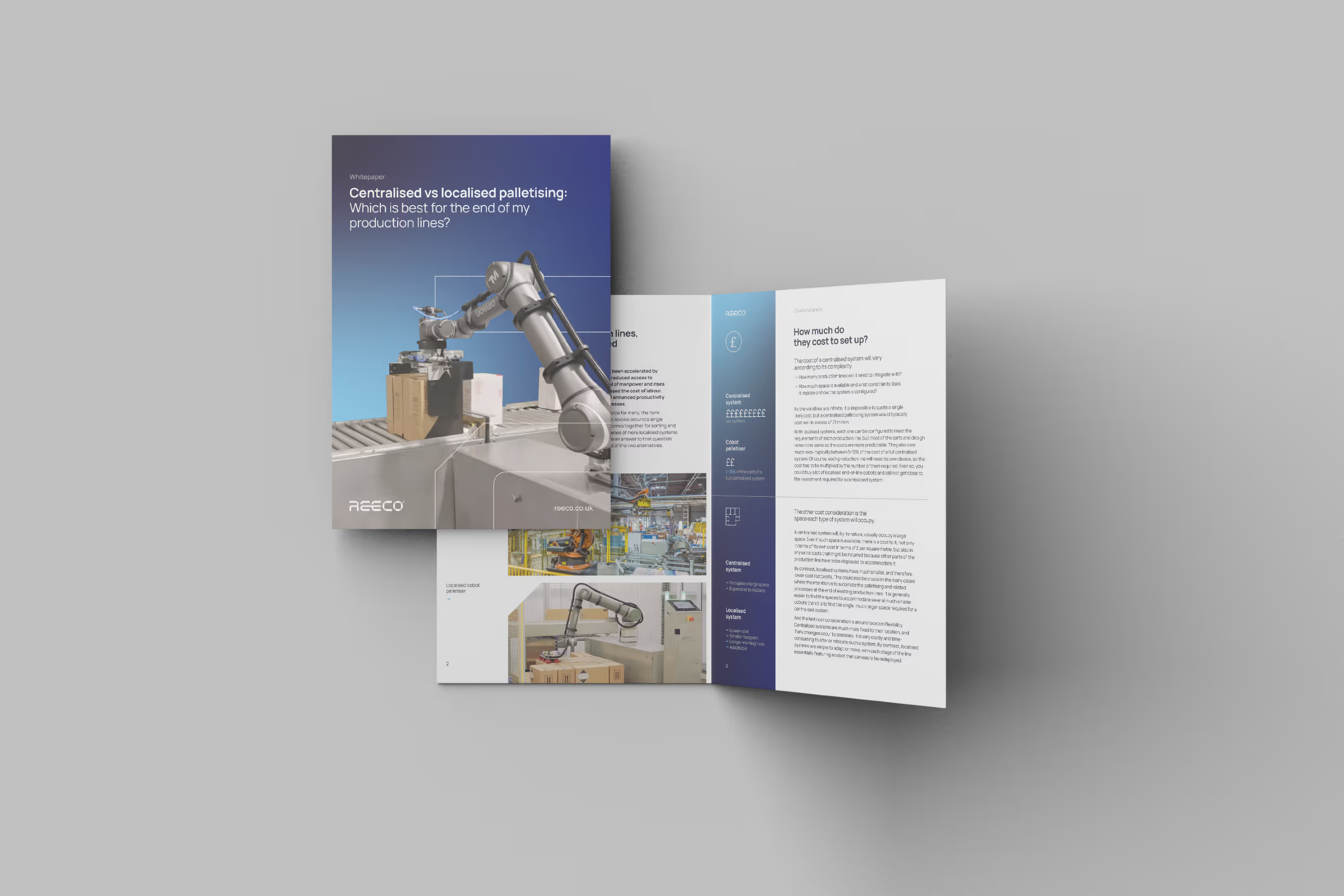