How Smart Palletising Software Reduces Operational Inconsistencies
With current market challenges such as labour shortage, keeping hold of skilled workers may prove to be more difficult than it previously was. When we combine this with statistics such as a 46.1% staff turnover within warehousing compared to a 12-15% average across the board as reported by the US Bureau of Labour Statistics, manufacturers may face operational inconsistencies. So how do we combat this?
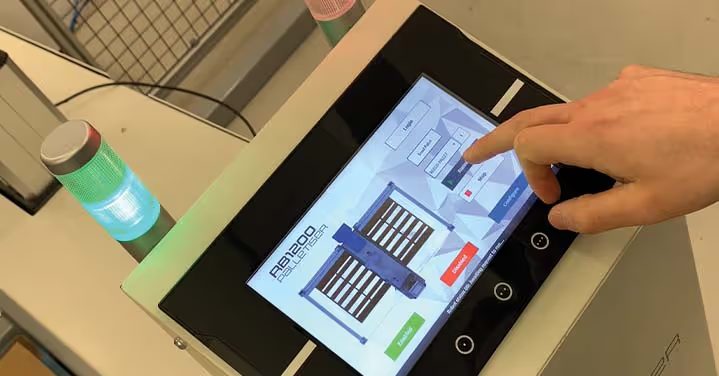
Simplifying operations through software
One method of simplifying operations is through software and the way we interact with machines, equipping them with the means of being operated quickly and easily by staff of any skill level.
While robots and technology alike advances, their accessibility continues to improve. In recent times there has been much discussion around smart software and how we interact with our machines. Customised and interactive user interfaces enable manufacturers to increase machine functionality and efficiency by combining all relevant hardware features into one visually intuitive display.
Three Problems Solved with the Help of Smart Software
We’ve touched on the issue of labour and staff turnover, but what are some of the other issues which cause inconsistencies and delays in day-to-day operations, and how does smart software help solve these issues?
1. Staff training can be a lengthy process, new staff will have to spend significant amounts of time understanding new and existing equipment, particularly the likes of agency workers, to ensure they are well connected with what’s happening on the factory floor. By simplifying user interfaces, we are able to significantly slash the training time required, reducing the pressure provided by high staff turnover.
2. Deployment of new equipment is complex, often requiring lots of engineering minds and programming time to reconfigure and redeploy. By having modular systems such as the RB1200 palletiser, in combination with smart software, we are able to move and repurpose equipment with much less time and resources.
3. Its likely that if you’re a manufacturer you have lots of different equipment from different suppliers, often arranging costly engineering call outs where you need support, or frantically trying to get hold of your engineering manager to come and fix the issue. A well-designed interface can combat this, dramatically reducing the skill level required and ensuring your equipment can be utilised as a tool by all levels of seniority, giving control back to the manufacturer.
The Benefits of Smart Software in Robotic Palletising
Almost any producer of large volume, particularly those in areas like Food and Commodities, are likely to have some form of palletising process where finished product is prepared for shipment. Automating these processes with palletising systems is the obvious quick way to ensure end of line consistency, but how can we reap even more benefits from the same systems?
Easy Stack is a software development by Reeco and Omron for the RB1200 Palletiser which simplifies palletising processes dramatically, combining the technology and capabilities of a palletising system into an easy to understand, visual programming tool.
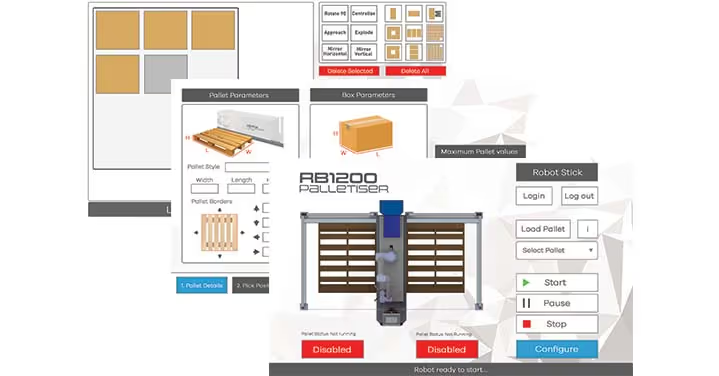
1. High SKU variability
High SKU variability is a challenge faced by many Food & Commodity manufacturers, often expanding product lines, producing seasonal products or changing packaging which is cause for reprogramming and reconfiguring equipment on the ground to ensure demand is met. Programming interfaces like Easy Stack hand this capability back into the hands of the manufacturer, allowing for quick alterations and additions.
2. Complexity of Automation
High complexity of automation, for example a system with lots of individual components with their own programming languages/manuals, often calls for further inhouse technical capability to respond to any hiccups. Systems like Easy Stack combine all these technologies into one central tool, providing a visually intuitive umbrella for all the RB1200’s features to live within.
3. On-demand Changes
Where traditional automated palletising systems may be initially setup to meet a particular demand/requirement at the time, changes to the system aren’t easily made, what if you want to test a higher speed now that your up-stream throughput has improved? Easy Stack allows you revisit any of your previously built pallets, edit and test individual parameter changes, giving you the opportunity to optimise on the fly.
The RB1200 palletiser is the latest offering in palletising technology, offering a cost reduction of up to 50% and a 60% smaller footprint when compared to conventional palletisers.
_
Speak to the specialists
To find out more about how Reeco can transform your end of line productivity, please call our head office on 01686 621 138, or email sales@reeco.co.uk.
You may also be interested in
Centralised vs localised palletising: Which is best for the end of my production lines?
The move towards end-of-line automation has been accelerated by changes in the labour market post-Brexit. The reduced access to overseas workers has resulted in a smaller pool of manpower and rises in the statutory minimum wage has also increased the cost of labour. This has all added to the existing arguments of enhanced productivity and reliability for switching to automated processes.
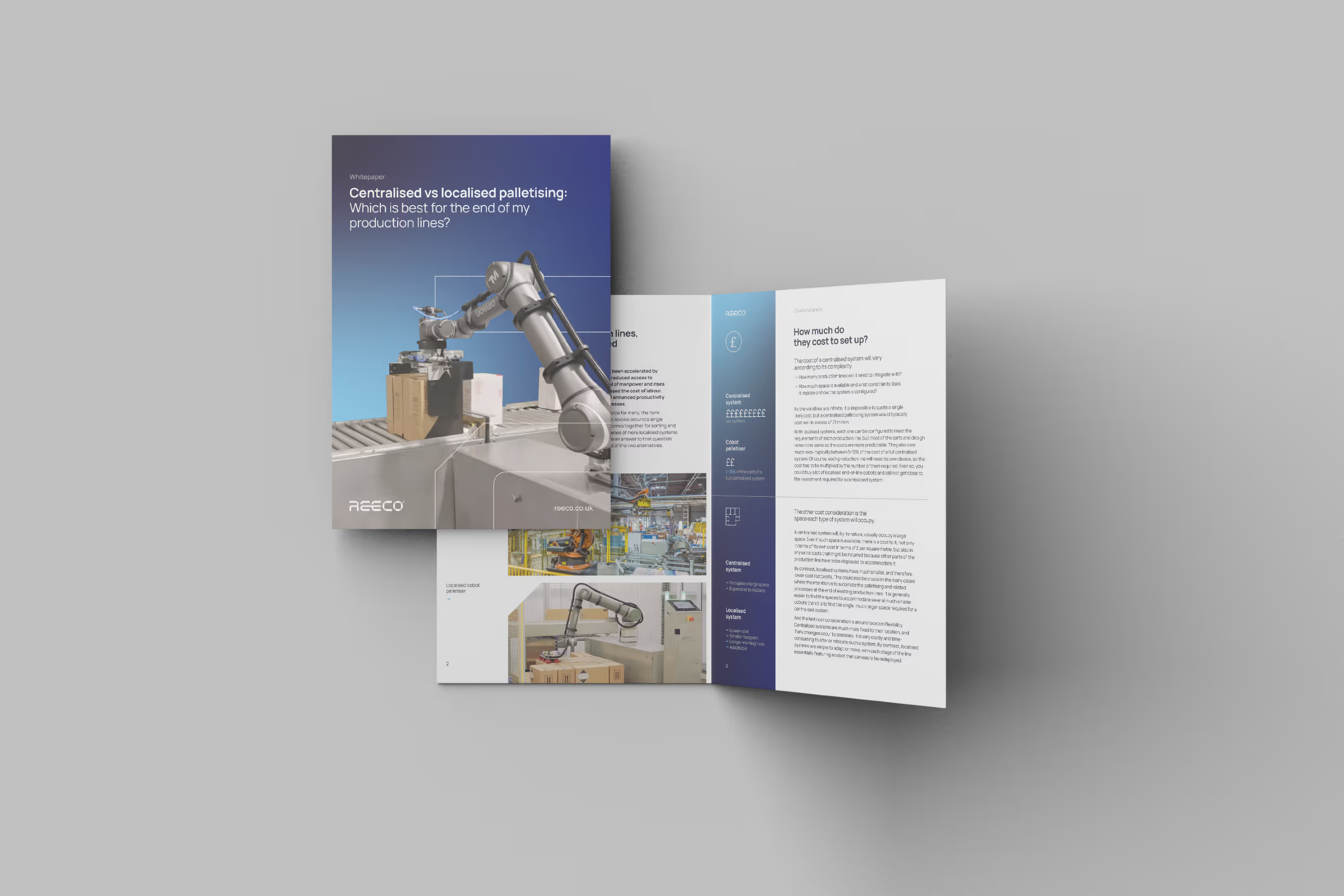