Pallet handling in intralogistics – What are the options?
Palletising is a fundamental process for nearly all manufacturing operations, whether automated or done manually. Goods produced by manufacturers will need to be transported and distributed, pallets are the preferred method due to their ease of handling and ability to neatly contain large volumes of product. The palletising process is where production ends and logistics begins, making it one of the core enablers for implementing an efficient means of moving product, enter intralogistics. Intralogistics is the internal management and movement of goods within a facility and can be a significant challenge to overcome. Intralogistics is an essential element of supply chain management, its structure and organisation directly reflects a company’s ability to reliably fulfil orders.
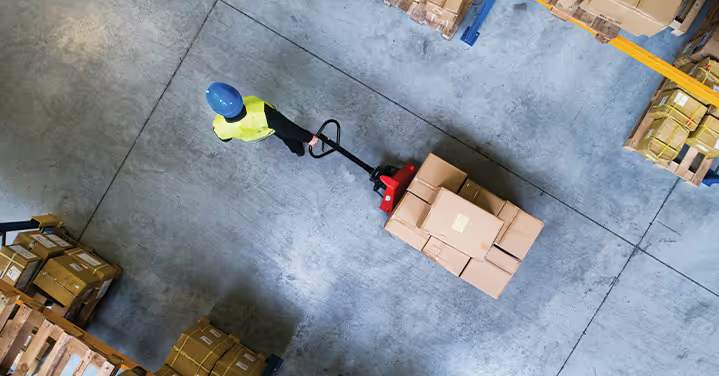
Why is intralogistics so important in 2022?
Health & Safety: As we progress as a society, the importance of health and safety continues to grow in parallel. Employee safety is the number one concern for many manufacturers, almost always presenting challenges. Intralogistics is one of the biggest safety hurdles to overcome, with people, forklifts and machinery often simultaneously moving material within restricted amounts of shared space.
Buyer Behaviour: Product life cycles are becoming shorter and shorter. Many companies are altering and expanding product ranges at an increasing rate in order to diversify and remain competitive. Buying behaviour is changing and consumer expectations are rising, overcoming these challenges requires a thorough analysis of both upstream and downstream operations, intralogistics is the link between the two which keeps material flowing.
Cost: The last mile of product delivery represents 41% of the total supply chain costs for a product. To combat this, many companies are launching micro fulfilment centres to make the last mile shorter and bring products closer to consumers, warehouses that deploy an effective intralogistics approach will be prepared to take advantage of this trend. Automating key processes such as end-of-line (EOL) pallet handling, warehousing and improving overall operational agility within high movement areas will ensure things run like clockwork, allowing for seamless order fulfilment without disrupting core operations.
End-of-Line pallet collection and delivery
No matter how you’re moving product, whether you’re doing it by hand, with pump trucks or with forklifts, EOL pallet collection and delivery is an area of intralogistics which requires high maintenance to avoid disruptions to production and distribution.
What are some of the challenges with pallet collection and delivery?
Pallet Safety
Full pallets are generally heavy, so when accidents occur can have serious implications. Falling pallets is an issue which has caused numerous fatal accidents, however the risks presented by falling pallets are often overlooked. Accidents caused by falling pallets are usually attributed to:
- The pallet itself, i.e poor construction & material
- Improper use, such as wrong pallets for the wrong loads
- Unsafe stacking which results in failing stacks/pallets
- Bad handling techniques
Most of these issues can be avoided by developing and implementing a safe and efficient approach to intralogistics, ensuring factory operations run as intended.
Forklifts
Forklifts are one of the most widely used solutions for intralogistics in the UK, although they still pose a huge challenge for health & safety, as highlighted by the following statistics:
- 1 in 5 workplace injuries are caused by a forklift truck or industrial vehicle
- 27 people are killed in forklift truck accidents at work every year
- 1,500 injuries are caused by forklifts and other industrial vehicles every year
Developing a strategy that allows for coexistence of vehicles and operators in the same environment is no easy task. In addition, the confederation of British industry (CBI) has identified forklift drivers as one of the hardest hit areas of UK labour shortage, further amplifying the issue.
The UK Health and Safety Executive suggest there are three key areas to consider when risk assessing and developing a watertight strategy:
- Safe Site
- Safe Vehicle
- Safe Driver
With consumer expectations rising and restrictions getting righter, maybe its time to change your approach?
Autonomous Mobile Robots (AMRs)
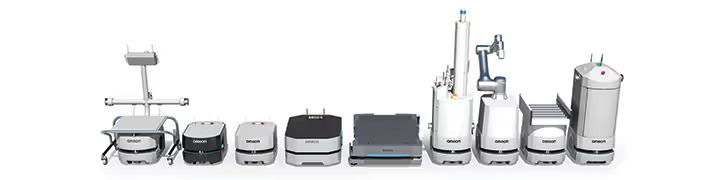
AMRs are the collaborative robot (cobot) of the mobile robot world. Safety is at the core of their design, their onboard laser systems enable them to scan and map their environment for seamless navigation of any factory floor autonomously and with zero assistance. Using obstacle avoidance technology, AMRs can quickly adapt and plan alternative paths should an obstacle enter its planned route, allowing them to navigate safely without unnecessary stoppages.
AMRs are an approach to intralogistics which don’t compromise safety.
Pallet handling with the RB1200+
The RB1200 from Reeco and Omron is a revolutionary, market-ready palletising system which offers superior operational flexibility and overall equipment effectiveness thanks to its intuitive software and modular design.
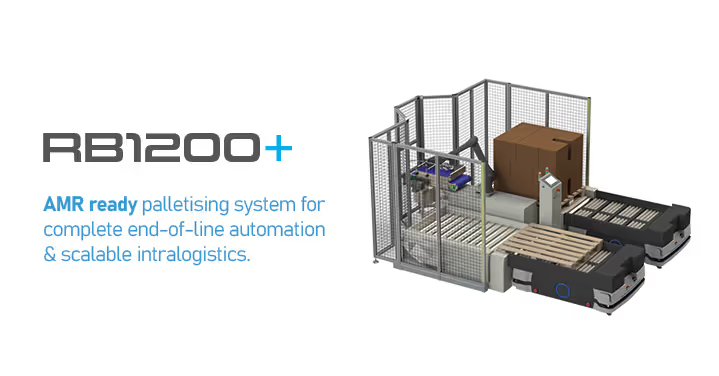
What about pallet handling? Enter the RB1200+. The RB1200+ is an AMR ready palletising solution, equipped with all the additional functionality required to transport pallets at the end of line by using the latest in AMR technology, the Omron HD1500 Mobile Robot.
The RB1200+ provides manufacturers with robotic pallet stacking precision while offering an open door into end of line pallet handling and scalable intralogistics with Omron AMRs.
- Reduce workplace accidents
- Dramatically increase productivity
- Improve your flexibility with agile infrastructure
- Eliminate errors
- Ease labour challenges
_
Speak to the specialists
To find out more about how Reeco can transform your end of line productivity, please call our head office on 01686 621 138, or email sales@reeco.co.uk.
You may also be interested in
Centralised vs localised palletising: Which is best for the end of my production lines?
The move towards end-of-line automation has been accelerated by changes in the labour market post-Brexit. The reduced access to overseas workers has resulted in a smaller pool of manpower and rises in the statutory minimum wage has also increased the cost of labour. This has all added to the existing arguments of enhanced productivity and reliability for switching to automated processes.
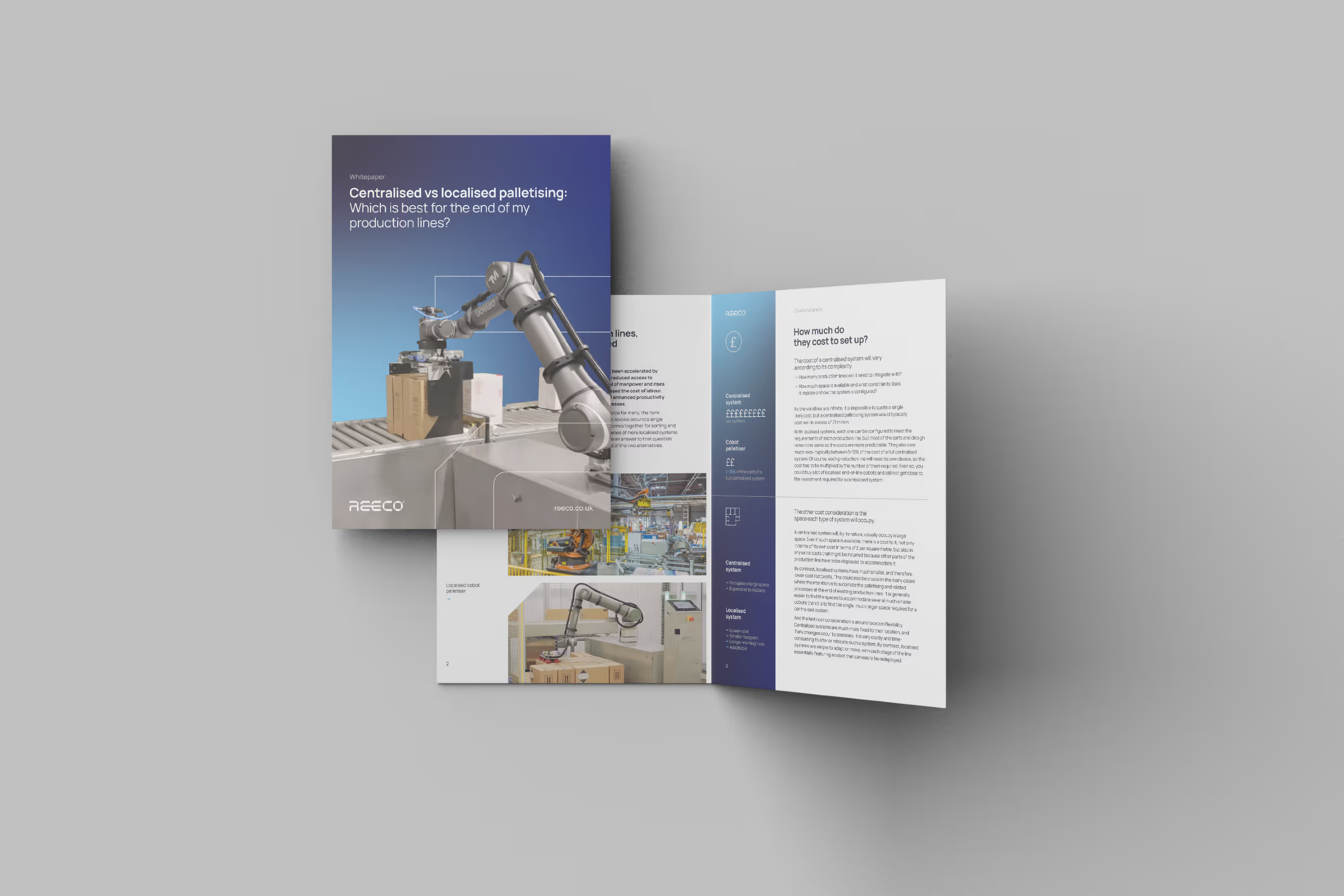