Slip Sheet Automation – Things you need to know
When it comes to palletising, a lot goes into ensuring everything runs smoothly, from the many upstream processes to the palletising task itself. One of those tasks could be placing a slip sheet between product layers – sounds minor, right? The thing with slip sheets is that in some cases they are critical to pallet strength. Pallets of delicate product or inadequate stacking strength alone (lots of small boxes or products with a slippery surface) are prime examples.
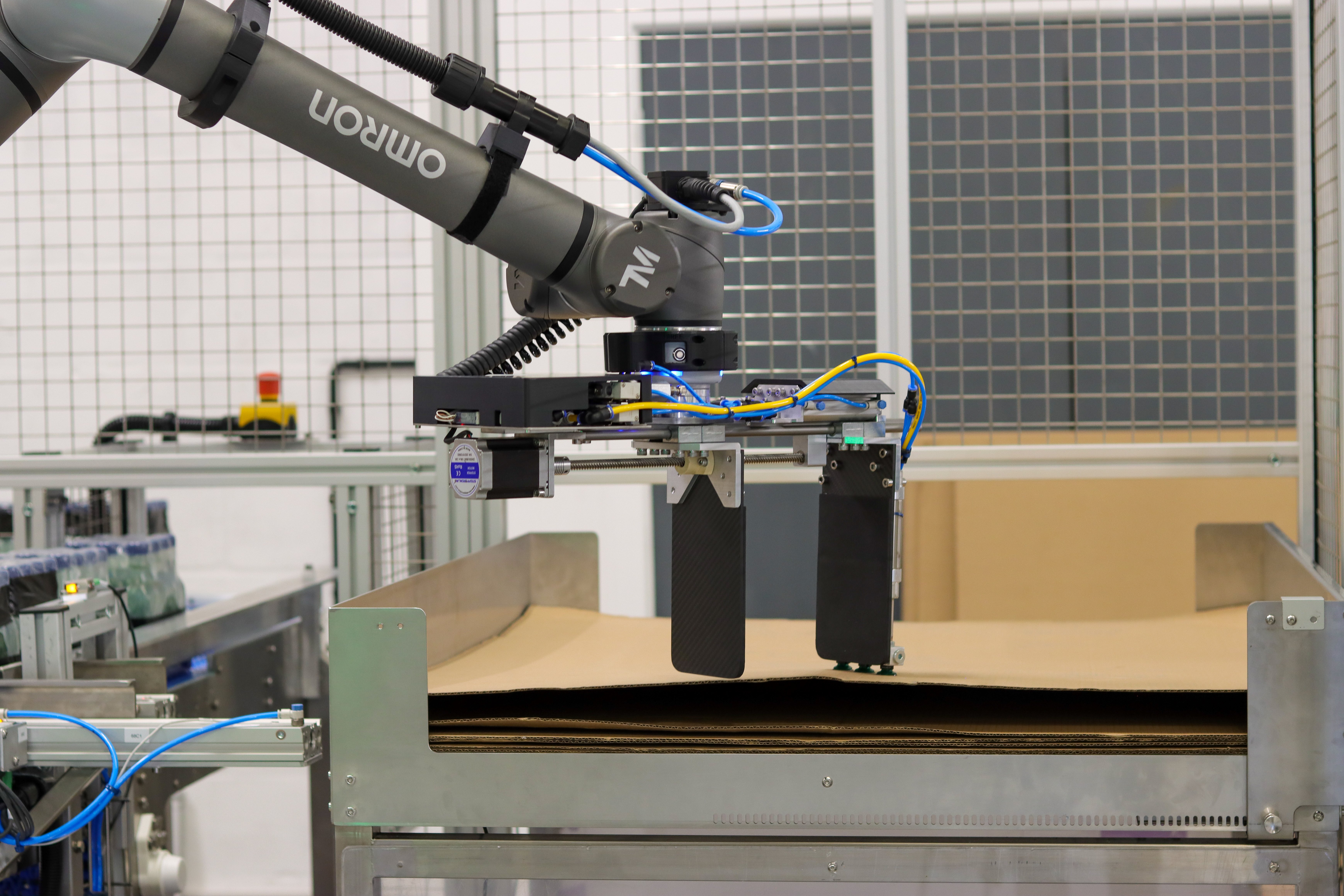
Contents
Slip sheets – a common oversight?
If you’re manually palletising and looking to automate, great! The good news is that there’s lots of solutions to choose from.
My slip sheets won’t be a problem though, right?
Technically no, but not all systems are suited to slip sheet application.
I mean sure there’s lots of capable solutions on the market, or even separate solutions for palletising and slip sheets, but that seemingly minor piece of card may throw a spanner in the works for the shiny new kit you originally had your eyes on.
Slip sheets are often an afterthought when it comes to palletising, you may even look for reasons to get rid of them so you can keep your original plan, but sometimes it’s not possible.
What are my options then?
Gantry Systems
In simple terms a gantry system is a frame with moving components that transports loads on a rail from A to B. They can be used on large scale for palletising and on smaller scales for slip sheet dispensing. Processes with minimal change and part orientation are best for this kind of automation.
Bespoke Systems
You could go down the bespoke slip sheet automation route, there is (almost) always a solution within reach if some good planning and design is put into practice. A bespoke solution would be moulded to your requirements and great at performing the task it was designed for.
Robotic Systems
Robots are a popular choice for palletising, their free movement means they can generally pick and place product how and wherever necessary. Depending on the vendor / integrator, robot palletisers may or may not include slip sheet functions, so in some cases you may still have to go down the bespoke route, however those that are geared for slip sheet will benefit from the flexibility of a robot arm.
Let’s take a look at a robotic example…
Slip sheets with a Cobot Palletiser
Industrial robots are very established in palletising, they have been used successfully for decades across many industries. Collaborative Robots (Cobots) are a newer solution, their success in palletising comes from their accessibility to new users and companies of all sizes.
Being newer, Cobot palletisers have slightly refreshed the robotic approach to slip sheet application, preserving their small footprint and user accessibility.
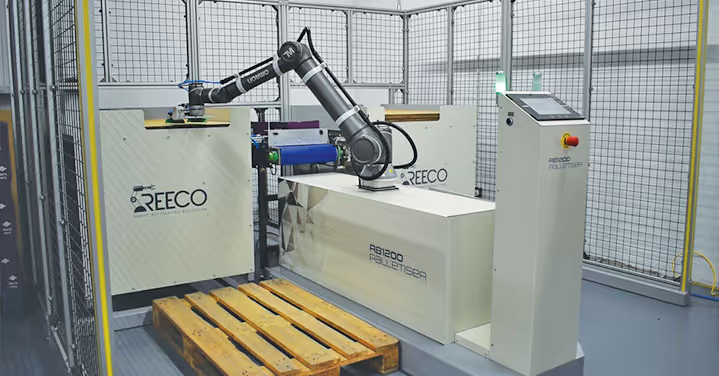
How does it work with a Cobot?
Cobot palletisers are intentionally small and compact, this design is no different with slip sheet automation.
Slip sheets are placed in a magazine located close to the robot so they can be easily accessed, the robot will pick directly from the magazine and place a sheet on top of the pallet between each layer cycle.
Slip sheet magazines come in all different shapes, sizes and orientations, but their purpose is the same, to store sheets ready for the robot to pick.
How do I refill the sheets?
The way you interact with your system depends on its safety design.
Systems which are ISO compliant will either need to be stopped, slowed, or have access from outside the guarded area in order to replenish slip sheets.
Well-designed Cobot Palletisers will typically have a front opening for pallet retrieval and replenishment which is monitored by safety scanners, the remainder of the cell sectioned off with physical guarding.
Slip sheet magazines can protrude the exterior guarding and provide limited access for operators to safely replenish sheets through a ‘letter box’.
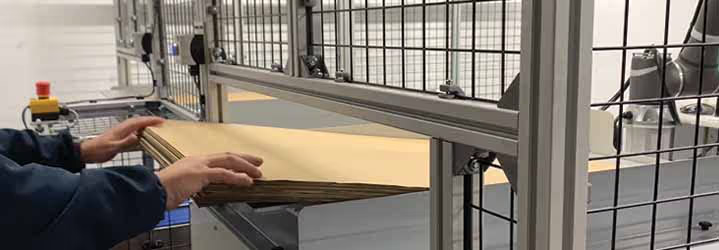
Using different slip sheets
If you palletise multiple different product types (SKUs), you may require different styles of slip sheet for each pallet (card, paper, foam etc). In this case you’d need to operate in one of two ways:
- Make use of a system that has one slip sheet magazine, running one product at a time and changing sheets in parallel with production.
- Use a system that has more than one slip sheet magazine, for example one for each pallet bay, filling each with the appropriate sheet and allow the system to palletise different products on each side.
Programming slip sheets
Things are always subject to change, you may want to remove slip sheets, change their configuration or even put them on new pallets, so how can you achieve this with a robot?
For robotic systems, slip sheet application is essentially a simple pick and place movement that’s integrated into each pallet program.
If you have inhouse capabilities, you may be able to configure these changes yourself with some programming knowledge.
Alternatively, you could call on some outside help from the original manufacturer, another robot specialist, or even upskill your team with some cobot training.
Some systems may also have slip sheet programming built into their user interface, for example the Easy Stack platform has full customisation throughout the entire pallet build, including slip sheet programming, so your average operator can manage the switch over.
Implementing automation in your business
Everyone can benefit from low-cost automation, even rental options are becoming available for those needing a temporary solution.
What should you consider when you want to automate your palletising?
- Define which tasks are the best to automate, the sooner you install, the sooner you begin generating a return on investment, start simple but start the process now.
- Weigh up different solutions. There are a variety of different solutions on the market, some easier to deploy than others. Ease of use and staff training is something to consider for future use and training up new operatives.
- Take into account future automation plans. You may have new products coming, packaging changes or even a need to redeploy equipment to a different line. Consider what future changes you’d need the flexibility to accommodate.
_
Speak to the specialists
To find out more about how Reeco can transform your end of line productivity, please call our head office on 01686 621 138, or email sales@reeco.co.uk.
You may also be interested in
Centralised vs localised palletising: Which is best for the end of my production lines?
The move towards end-of-line automation has been accelerated by changes in the labour market post-Brexit. The reduced access to overseas workers has resulted in a smaller pool of manpower and rises in the statutory minimum wage has also increased the cost of labour. This has all added to the existing arguments of enhanced productivity and reliability for switching to automated processes.
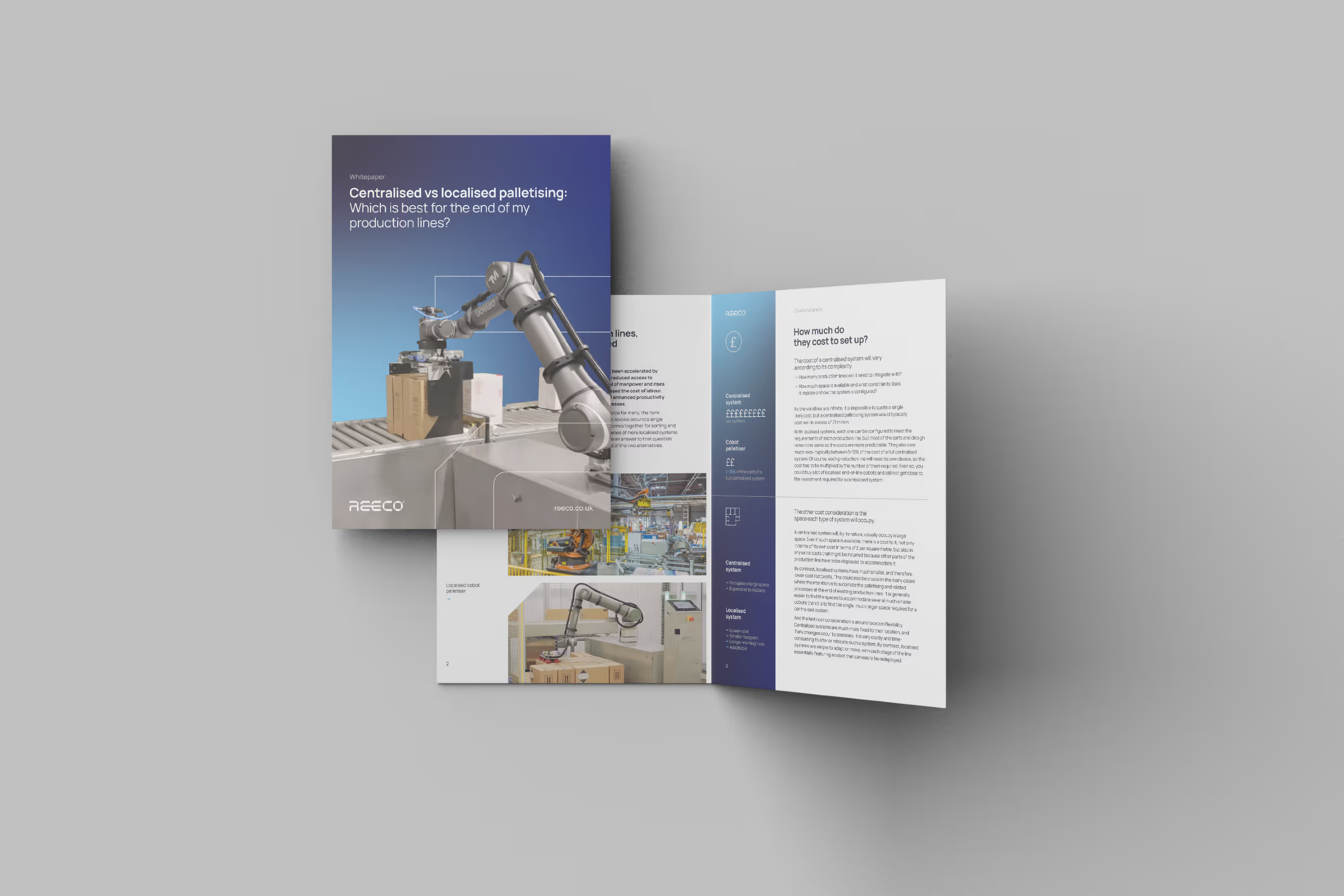